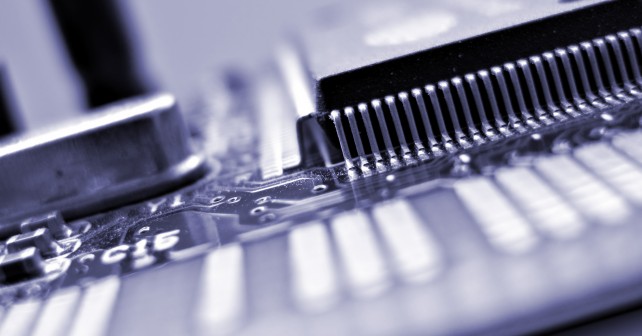
What is SMT?
The vast majority of commercial electronics are all about complex circuitry fitting in small spaces. To do this, components need to be directly mounted onto the circuit board rather than wired. This is essentially what surface mount technology is.
Is Surface Mount Technology important?
A huge majority of today’s electronics are manufactured with SMT, or surface mount technology. Devices and products that use SMT have a large number of advantages over traditionally routed circuits; these devices are known as SMDs, or surface mount devices. These advantages have ensured that SMT has dominated the PCB world since its conception.
Advantages of SMT
- The main advantage of SMT is to allow automated production and soldering. This is cost and time-saving and also allows for a far more consistent circuit. The savings in manufacturing costs are often passed along to the customer – making it beneficial for everyone.
- Less holes need to be drilled on circuit boards
- Costs are lower than through-hole equivalent parts
- Either side of a circuit board can have components placed on it
- SMT components are far smaller
- Higher component density
- Better performance under shake and vibration conditions.
Disadvantages of SMT
- Large or high-power parts are unsuitable unless through-hole construction is used.
- Manual repair can be extremely difficult due to the extremely low size of components.
- SMT can be unsuitable for components that receive frequent connecting and disconnecting.
What are SMT devices?
Surface mount devices or SMDs are devices that use surface mount technology. The various components used are designed specifically to be soldered directly to a board rather than wired between two points, as is the case with through hole technology. There are three main categories of SMT components.
Passive SMDs
The majority of passive SMDs are resistors or capacitors. The package sizes for these are well standardised, other components including coils, crystals and others tend to have more specific requirements.
Integrated circuits
For more information about integrated circuits in general, read our blog. In relation to SMD specifically, they can vary extensively depending on the connectivity needed.
Transistors and diodes
Transistors and diodes are often found in a small plastic package. Leads form connections and touch the board. These packages use three leads.
A brief history of SMT
Surface mount technology became widely used in the 1980s, and its popularity has only grown from there. PCB producers quickly realised that SMT devices were much more efficient to produce than existing methods. SMT allows for production to be highly mechanised. Previously, PCBs had used wires to connect up their components. These wires were administered by hand using the through-hole method. Holes in the surface of the board had wires threaded through them, and these, in turn, connected the electronic components together. Traditional PCBs needed humans to assist in this manufacture. SMT removed this cumbersome step from the process. Components were instead soldered onto pads on the boards instead – hence ‘surface mount’.
SMT catches on
The way that SMT lent itself to mechanisation meant that usage spread quickly throughout the industry. A whole new set of components were created to accompany this. These are often smaller than their through-hole counterparts. SMDs were able to have a much higher pin count. In general, SMTs are also much more compact than through-hole circuit boards, allowing for lower transportation costs. Overall, the devices are simply much more efficient and economical. They are capable of technological advances that could not have been imaginable using through-hole.
In use in 2017
Surface mount assembly has almost total domination of the PCB creation process. Not only are they more efficient to produce, and smaller to transport, but these little devices are also highly efficient. It is easy to see why PCB production has moved on from the wired through-hole method.
Looking for a quote for surface mount assembly? Get in touch with the experts at PCB Train today.
Leave a Reply